AET are proud to supply the all new Biax oil free grinder. With the new oil-free T 3-90 S, BIAX is setting new standards in terms of precision, working comfort and machining results.
Achieve excellent surface results with the finest deburring and grinding work at 90,000 rpm. Experience grinding with incredibly low effort – the slim, graceful device with a diameter of just 22 mm sits very comfortably in the hand and runs extremely smoothly and quietly.
The spindle is completely decoupled from the housing and equipped with a paired floating bearing at the front – this prevents vibrations from occurring in the first place and ensures maximum precision during grinding, while at the same time guaranteeing excellent wear resistance. A run-out brake provides additional safety when switching off. Variable air consumption for reduced energy costs: the air consumption is automatically decreased with a reduced load.
BIAX is a trademark of Schmid & Wezel, a Swabian family company founded in 1919. They have always developed and produced high-precision and high quality pneumatic and electric tools. All of their machines are manufactured in Germany and Switzerland and are tailored to the needs of the metalworking industry. Their wide range of hand-held air grinders offers the perfect solution for almost any deburring or grinding task. They offer a wide range of stationary pneumatic spindles with and without deflection for automated processing with robots or CNC machines. The BIAX range is rounded off by their other products such as pneumatic filers, saws, chisels, drills, electric scrapers, machines with flexible shafts and carbide tools – all proudly supplied by Aersoapce and Engineering Tools Ltd. Call +44(0)1204365120 to find out more.
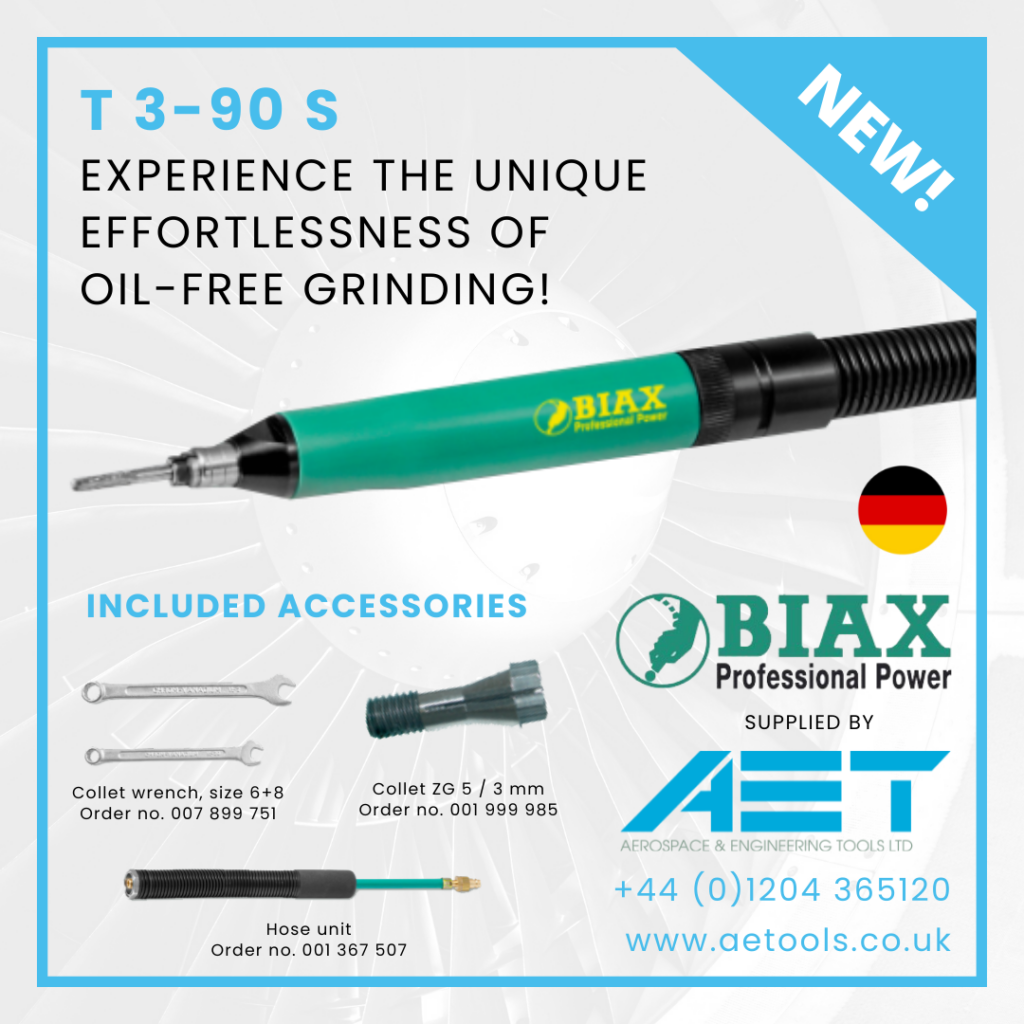